Table of Contents
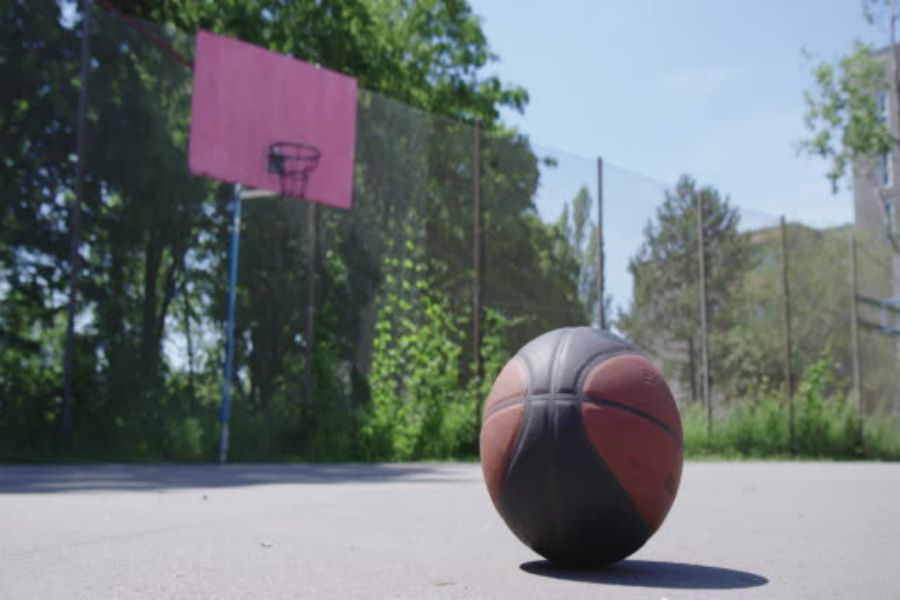
The History of Rubber Basketballs
Rubber basketballs have been a staple in the game of basketball for decades. These versatile and durable balls have revolutionized the sport, allowing players to dribble, shoot, and pass with ease. In this article, we will take a behind-the-scenes look at how rubber basketballs are made, from the materials used to the manufacturing process.
The Composition of Rubber Basketball
Rubber basketballs are made up of several key components. The outer shell is typically made from synthetic rubber, which provides grip and durability. Inside the ball, there is a bladder, usually made from latex or butyl rubber, which holds the air. The bladder is then surrounded by layers of fabric or nylon windings, which give the ball its shape and structure.
The Manufacturing Process
The manufacturing process of rubber basketballs involves several steps, starting with the preparation of the materials. Synthetic rubber is mixed with various additives, such as carbon black and stabilizers, to improve the ball's grip and durability. The mixture is then heated and shaped into sheets, which will later become the outer shell of the ball.
Cutting and Shaping the Panels
Once the rubber sheets have been prepared, they are cut into panels. These panels are typically hexagonal or octagonal in shape and are carefully measured to ensure consistency and accuracy. The panels are then molded into the desired shape using heat and pressure.
Assembling the Ball
After the panels have been cut and shaped, they are ready to be assembled into a basketball. The panels are stitched together using a strong nylon thread, which provides added strength and durability. The bladder, which holds the air, is then inserted into the ball, and the opening is sealed tightly.
Quality Control and Testing
Before rubber basketballs are ready for the market, they undergo rigorous quality control and testing. Each ball is inspected for any defects, such as uneven panels or stitching. The balls are also tested for bounce, grip, and air retention to ensure they meet the required standards.
Addition of Graphics and Branding
Once the rubber basketballs pass the quality control tests, they are ready for the final touches. Graphics and branding, such as the manufacturer's logo and the ball's design, are added using a variety of techniques, including screen printing or heat transfer. These graphics not only enhance the ball's appearance but also serve as a way to promote the brand.
Packaging and Distribution
After the rubber basketballs have been manufactured and branded, they are packaged and prepared for distribution. The balls are typically stored in boxes or mesh bags to protect them during transportation. They are then shipped to retailers, sports stores, and online platforms, where they are made available for purchase by basketball players and enthusiasts worldwide.
Maintenance and Care Tips
Proper maintenance and care can extend the lifespan of a rubber basketball. It is recommended to store the ball in a cool, dry place and avoid exposure to extreme temperatures. Regular cleaning with mild soap and water can help remove dirt and debris. Additionally, keeping the ball properly inflated and avoiding sharp objects or rough surfaces can prevent damage.
Conclusion
Now that you have a behind-the-scenes look at how rubber basketballs are made, you can appreciate the craftsmanship and precision that goes into creating these essential sporting goods. From the selection of materials to the assembly and testing process, every step is crucial in ensuring the quality and performance of rubber basketballs. So, the next time you pick up a basketball, remember the intricate process that brings it to your hands.